![]()
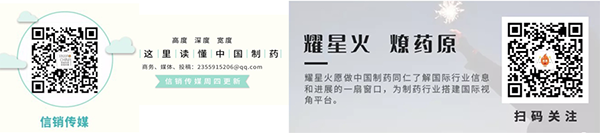
作者:高志强
阅读此文,深入了解发酵工艺的无菌保障原理及灭菌方式的选择,洞析整个发酵车间及系统的设计理念,从此同类项目,执行起来得心应手。
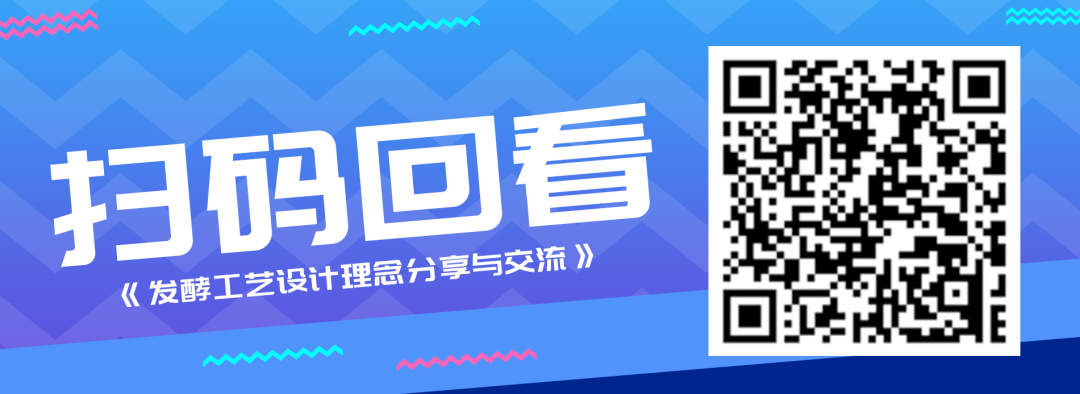
天俱时工程科技集团有限公司智能制造装备事业部总工程师高志强先生在+1大会·云—国际制药产业云峰会“连续制造专场论坛”分享《发酵工艺设计理念分享与交流》。本文根据嘉宾报告内容整理,经演讲嘉宾本人确认并同意公开分享。
传统发酵是指利用自然界存在的微生物或用传统方法改良的微生物来生产原料药的工艺。传统发酵工艺生产的原料药通常是小分子产品,如抗生素、氨基酸、维生素和糖类。
发酵染菌是指在发酵过程中,生产菌以外的其他微生物(也称杂菌)侵入了发酵液,从而使发酵过程失去了真正意义上的纯种培养。如果染入了杂菌产生了竞争,发酵的产物效价就会受到影响。在发酵染菌之后,必须分析染菌原因,总结发酵染菌的经验教训。把发酵染菌消灭在染菌之前,防患于未然,是积极克服发酵染菌的最重要措施。造成染菌的原因很多,但总结起来,其主要原因有:种子带菌、无菌空气带菌、设备渗漏、灭菌不彻底、操作失误和技术管理不善等。值得注意的是,不明原因的染菌高达25-35%。无菌保证是发酵工艺设计的重点。广义上的无菌保证工艺是指一切跟保证生产不受杂菌影响的相关措施,狭义上的无菌保证工艺核心就是灭菌。发酵行业生产中使用化学灭菌法比较少,主要用在无菌室和实验室等擦拭消毒。物理灭菌法有辐射、干燥、过滤、温度等方法。发酵生产中主要用的是过滤法和热力灭菌法,除菌过滤主要用于压缩空气,热力灭菌主要用于培养基和设备管道的消毒。热力灭菌分为干热灭菌和湿热灭菌。发酵生产工艺中以湿热灭菌应用比较多。一般情况下,蒸汽(灭菌)温度每升高10℃,灭菌速度常数将提高8-10倍。饱和蒸汽的穿透力是最强的,灭菌效果是最好的。经过研究表明,培养基中微生物的热致死速率与残存的微生物的数量是成正比,符合对数残留定律。
![]()
式中:
热致死速率常数K值越大,微生物的热致死速率越快,所需的灭菌时间越短。K值是微生物耐热性的表征,与微生物的种类和灭菌温度有关。根据阿伦尼乌斯方程可以得到,热致死速率常数和灭菌温度之间的关系式,从而计算不同微生物在不同温度下灭菌的时间。
由前面两个公式得:
该方程对于每一个不同的微生物的A和Ea都是不同的,但是工程问题可以简单化,灭菌都是过度灭菌,只要找到最常遇见的最难灭杀的微生物的A和Ea即可。在发酵工业中规定:以Nt=0.001为达到灭菌要求,即灭菌失败的几率为1/1000为达到要求。一般情况下,营养物质被破坏的活化能要低于微生物的致死活化能。所以得到结论:温度升高,对微生物致死速率的增速大于培养基营养成分破坏速率的增速。温度的升高更有利于提高微生物致死速率,减少灭菌时间。培养基灭菌应该遵循的是高温短时的原则,以保证灭菌的可靠性同时减少对培养基的破坏。原料药行业发酵过程中培养基的灭菌方式一般分为:分批灭菌的实消和连续灭菌法两种。分批灭菌法的优点是无需其他设备、操作简单,对蒸汽稳定性要求比较低,一般0.3-0.4MPa的蒸汽就可以满足使用。缺点是灭菌时设备利用率比较低,灭菌时间长,营养成分易遭到破坏,大型的发酵罐难以实现短时灭菌,一般适用于小型的发酵罐和种子罐的培养基的灭菌。连续灭菌也叫连消,连消经过多年的发展也出现了很多种形式。根据工艺是否允许蒸汽直接进入培养基,分为直接和间接加热的灭菌方式,直接加热用到连消塔、喷射器等设备,间接加热需用到加热器设备。另外,连消装备本身的消毒方式可以分为高压过热水消毒和蒸汽消毒两种,辅助其他不同的设计形式可以组成不同的连消系统。连消主要用于大规模发酵生产的液体培养基的灭菌,在维生素C和谷氨酸等的生产中应用广泛。糖和氮源物质在高温下发生变色反应,在7-ACA、红霉素等发酵生产过程中,把糖和氮源分开灭菌,葡萄糖单独连消后送入发酵罐,预热器的使用大大提高了连消工艺的节能意义和推广价值。一般情况下,连消过程中发酵罐必须要提前进行空消。空消灭菌一般是维持罐内压力在0.15-0.2MPa,罐温在125℃-130℃,维持时间是30-40min。空消蒸汽耗量一般情况下是按照5-10倍发酵罐的体积乘以空消压力下的蒸汽密度,可以计算出必要的蒸汽实际耗量。当然实际过程中,蒸汽耗量与发酵罐的形式和生产操作相关,有的发酵厂家的蒸汽耗量比理论值大的多。灭菌以后,为了避免罐压急剧下降造成负压,要等经过连续灭菌的无菌培养基进入罐体后,再打开循环水或冷却水进行降温。表一 连续灭菌和分批灭菌的对比
![]()
两种灭菌效果都是比较好的。连续灭菌的温度是130-144℃,分批灭菌是121℃。根据前面的阿伦尼乌斯方程的原理,连续灭菌是高温瞬时,分批灭菌是121℃灭菌30分钟。连续灭菌对培养基的破坏比较小,分批灭菌对培养基的破坏比较大。连续灭菌时需要的蒸汽压力要高于分批灭菌。连续灭菌对蒸汽和冷却水的负荷要求,瞬时量是比较平均,总量比较低,分批灭菌要求的瞬时量很高,总量也是比较高。操作的难易程度,连续灭菌一般情况下是根据自控稳定生产,分批灭菌是手动操作加热和降温,比较简单。消毒设备和动力投资,总体而言,使用时间越长,连续灭菌的总投资越低,分批灭菌越高。智能瞬时连消机是基于高温短时灭菌的原理,充分利用蒸汽潜热,经过新型的换热器做到纯逆流换热的灭菌设备。由维持器、喷射器、换热换(预热器)和自控系统组成。采用短时高温迅速灭菌的连消对培养期破坏小,培养基的色泽和灭菌前无明显差异。灭菌物料广泛,玉米浆和玉米粉等均可彻底灭菌。如果是淀粉含量比较高的物料,允许在今进入连消之前进行液化,50%左右的淀粉也可直接使用连消系统。
发酵车间简单来说就是用特定的微生物在特定的温度、压力、溶氧、PH的条件下生成特定的产物。发酵车间可分为几个系统:配料系统、连消系统、空压系统、蒸汽系统、循环水降温系统、补料系统、取样系统和移种系统,发酵车间工艺设计时,不同的系统要考虑不同的内容。厂房布局设计原则包括:模块化的组合,生产操作方便,减少染菌机率,降低环境湿度。工程措施中,垂直布局考虑物料输送及操作面整齐美观;水平布局按照模块划分;控制室应该设在视野开阔的区域,开设大的观察窗;保证无菌管道的顺畅;气候炎热的地区,一层是半敞开的,屋面设天窗加强通风。发酵车间的垂直布局一般是三层框架结构,只有当发酵罐体积特别大的时候做4层。
![]()
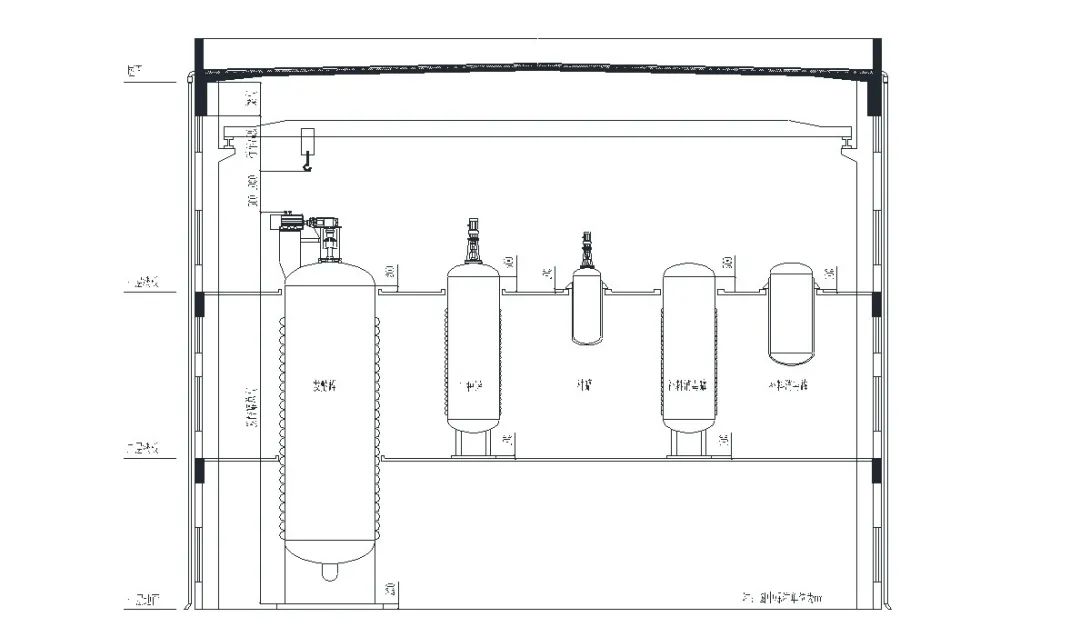
各层高确定原则:发酵车间建筑高度的确定首先是依据发酵罐从头到尾所有的高度关系,还要考虑室内外的高差和屋面建筑面层的厚度,总体建筑高度要小于24米,否则就会变成高层建筑。根据发酵罐的高度确定三层楼板的标高,以二级种子罐的高度确定二层楼板的标高,以发酵电机和检修行车高度,确定发酵车间的总建筑高度。结合对其他一级种子罐、补料罐等辅助设施的考虑,调整后确定楼板标高。
![]()
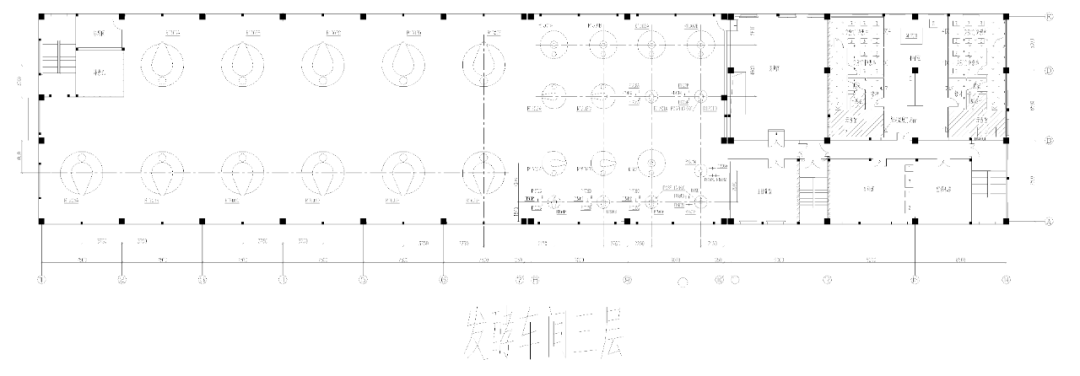
各层的布局原则:所有罐体上封头和操作面尽量都设计在三层,便于操作同时兼顾美观。除了罐体操作面,还设计有种子室和控制室,方便一级种子罐的接种和操作人员观察。因为工艺优化的过程中,一般情况下会加一些辅料罐或者其他的小设备,所以补料和种子罐的区域要留一些空间,方便以后加设设备或改造工艺。另外为了防止发酵搅拌对种子室内仪器的影响,一般情况下会设伸缩缝。二层设计霉菌室和化验室,因为取样一般在二层,方便取样以后送样化验。同时,配电室和变频室一般也设计在二层。为什么发酵车间的用电设备都在三层,而配电室要设在二层呢?因为三层有检修行车运行,需要抽取掉部分柱子,空间上对桥架的布置不方便。一层设计配料区域及设备管道。
传统的发酵原料药大多属于好氧液体发酵,好氧液体发酵罐的设计要点是:1、设计发酵罐首先是选择适宜的高径比,一般取1.8-2.8。发酵罐容积较小时,高径比宜取上限,容积较大时宜取偏下限。2、发酵罐除了维持正常的培养罐压,还要承受设备和培养基灭菌时的蒸汽压力。3、合适的通气搅拌方式,要使通入罐内的无菌空气能均匀分布,加强气液接触效果,提高氧气利用率,保证发酵液充分混合,料液浓度均一。4、另外需要考虑足够的换热面积,不同设计的盘管方式的换热效果是不一样的。5、无菌效果的保证,一般发酵罐是不锈钢的材质,内壁抛光是0.4-0.8μm,罐体内件尽量减少死角,搅拌装置应该有严密的轴封,防止泄漏,以保证设备能够灭菌彻底。应用较广泛的好氧液体发酵设备主要分为:机械搅拌通气式发酵罐和气升式发酵罐。机械搅拌通气式发酵罐能够保证气液充分混合,提高发酵液的溶氧量,利于传热,特别适合通气比要求较高、发热量大的发酵反应;但是内部的结构复杂,操作要求比较高,而且机械搅拌对于丝状细胞的培养有不利影响。气升式发酵罐是以气体搅拌,节省动力,设备投资降低约30%,没有机械剪切力,特别适合动植物细胞、维生素C的培养。但是对于粘度大的发酵液溶氧率较低,不适合固含量高、粘度大的发酵液。发酵罐内盘管设计,第一种上下缠绕管形式,第二种是蛇形缠绕形式,第三种是做成管排子。这三种不同的形式各有优缺点。上下缠绕管形式的发酵罐,不管是实消还是空消过程中,冷却水很难排干净,消毒时需要将存水也加热到消毒温度,使用的蒸汽量比别的形式多,同时也更容易染菌。蛇形管形式的优点是冷却水可以排干净,但是缺点是对设计盘管的长度精确度要求高,防止出现蛇管末端没有换热温差,造成换热面积的浪费。第三种管排子形式能把冷却水排干净,同时避免了没有换热温差的情况。这也是为什么在空消过程中,不同的厂家使用的实际蒸汽量存在较大区别的原因之一。根据甲方消毒工的习惯,不同的项目会用不同的移种管道。移种管道系统分为公用管道和分配站两种,两种形式各具优缺点。
![]()
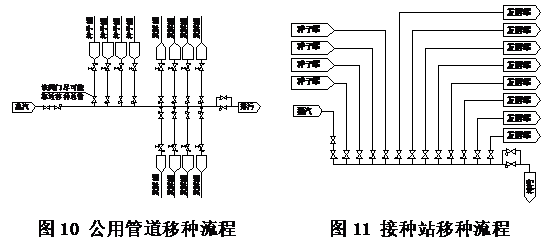
公用管道总管比较长,各个移种支管比较短,所有管道总用量比较小,车间布局比较简单。但是因为总管较长,非端头的两个罐子移种的时候,对发酵的种子液浪费比较多。各个阀门相对较远,人员走动比较多,操作不是很方便。在灭菌操作的时候,各个支管根部和总管连接处容易形成死角。如果每一个连接处都设小排气阀,车间冒蒸汽的地方就比较多。
![]()
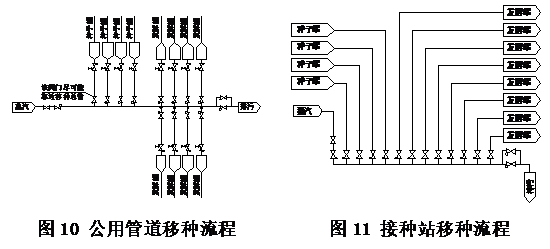
分配站是将罐子之间的移种阀门集中到一起,各个移种支管连接到一个较短的母管上。不进行操作时,母管是蒸汽汽封状态。它实现了移种的集中操作,减少了人员的走动,操作更加方便。母管较短,种子液浪费比较少,灭菌的效果也比较可靠。但是每一个支管比较长,总管耗量比较大,占的空间也比较多。发酵分配站的阀门应该布置在母管的上方,否则支管的根部就会容易存残种子液造成污染。补料管道同样分为公用管道和分配站的方式,补料公用管道的方式存在消毒的局限性,现已不常用(对于有抑菌作用的物料补加可以使用),推荐使用补料分配站方式进行补料。无菌管道是串联起发酵设备和管道系统的静脉和网络,这个管道在整个发酵车间里面焊接和设计是比较麻烦的,要对实际的流程图和施工现场进行反复推敲排污排气的位置,从而保证消毒的彻底。发酵用的压缩空气制备的处理过程;空气——过滤器——空压机——冷却器——汽水分离器——压缩的空气管线加热器——过滤——供应用点,一般情况下发酵车间的空气是经过总过滤器再分到不同的发酵罐,每一个发酵罐上面有空气的预过滤器和精过滤器,在消毒蒸汽进过滤器的时候,蒸汽要经过蒸汽过滤器。发酵排气分为消毒排气和培养排气。消毒排气主要是在空消和实消的过程中满足灭菌压力要求后排掉的乏蒸汽。消毒排气一般情况下是高温的,因此,对后面的排气管道是有要求的。培养排气一般情况下是在培养过程中的排气,主要是微生物产生的二氧化碳和代谢的废气,压力比较低,气量比较大。因此,两种排气系统需要分成不同的分支分别处理。
自动化控制的理念是无菌保证,保证无死角和0染菌;仪表要耐温、耐压、标准化,自动化的操作程序;节能环保,要精确的计量,调节要精确,密闭输送;数据采集完整,远传显示记录。发酵车间主要的监测参数有温度、罐压、进气流量、溶氧、PH值、泡沫、补料量和搅拌等参数。从源头上要省蒸汽,瞬时连消较实消节省蒸汽70%以上。物料经过预热器升温以后,节省了蒸汽的用量,高温的物料再到预热器里给低温的物料去预热。经过连消系统以后的出料温度,一般情况下在50-60℃,一般不需要再用循环水冷却。所有消毒都是在密闭环境中进行,所以避免了培养基在实消过程中消毒排气,将发酵味道散布到环境中。空气系统的设计中,从空压站出来的压缩空气一般情况下是高温的。通过两种方式回收热量。第一种形式是用高温的压空与要升温的压空(除湿以后的压空)换热。另一种是用水将压缩空气制备过程的热量收回来,在其他低品质热源厂区进行使用。
扫码回看内容:天俱时工程科技集团有限公司智能制造装备事业部总工程师高志强分享《发酵工艺设计理念分享与交流》。
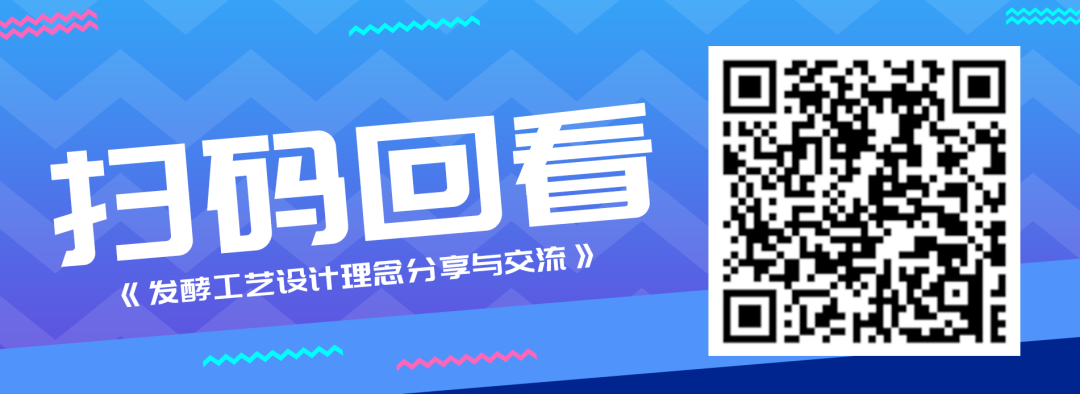
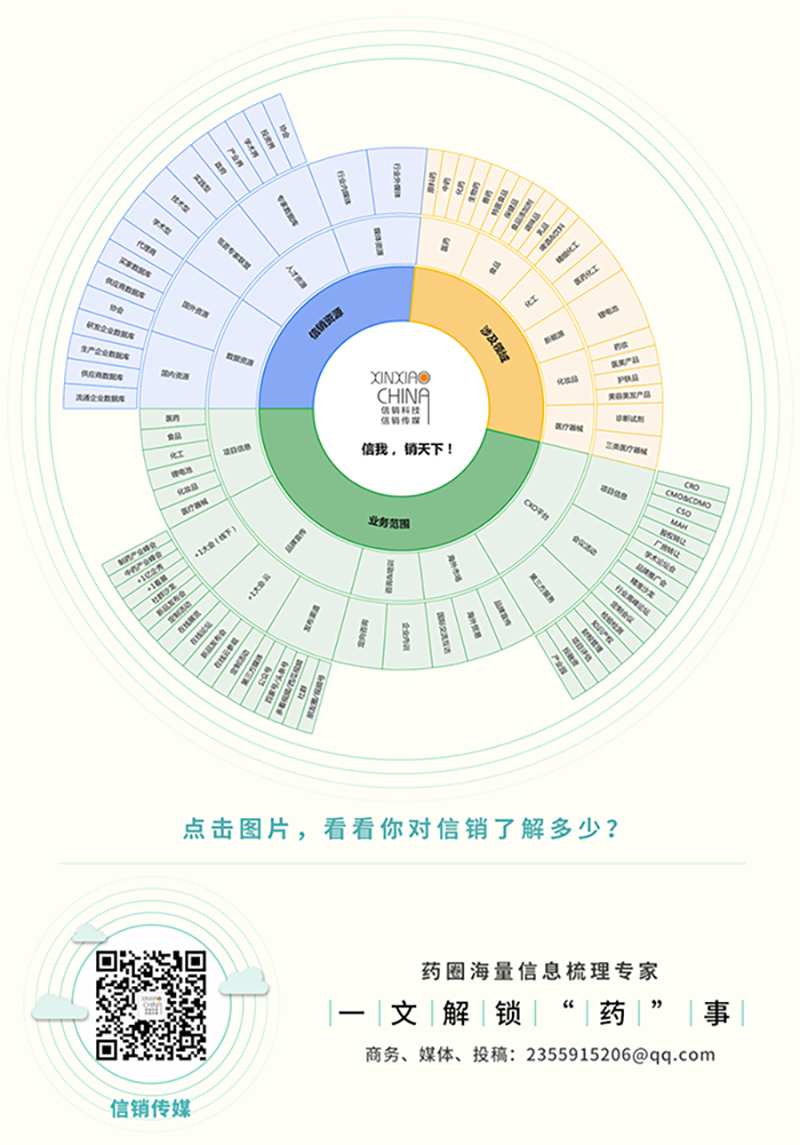
![]()
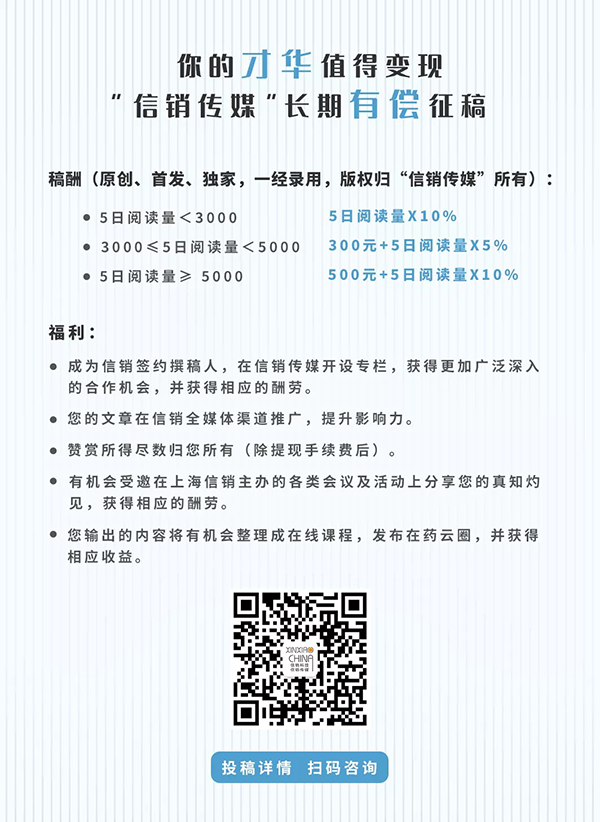